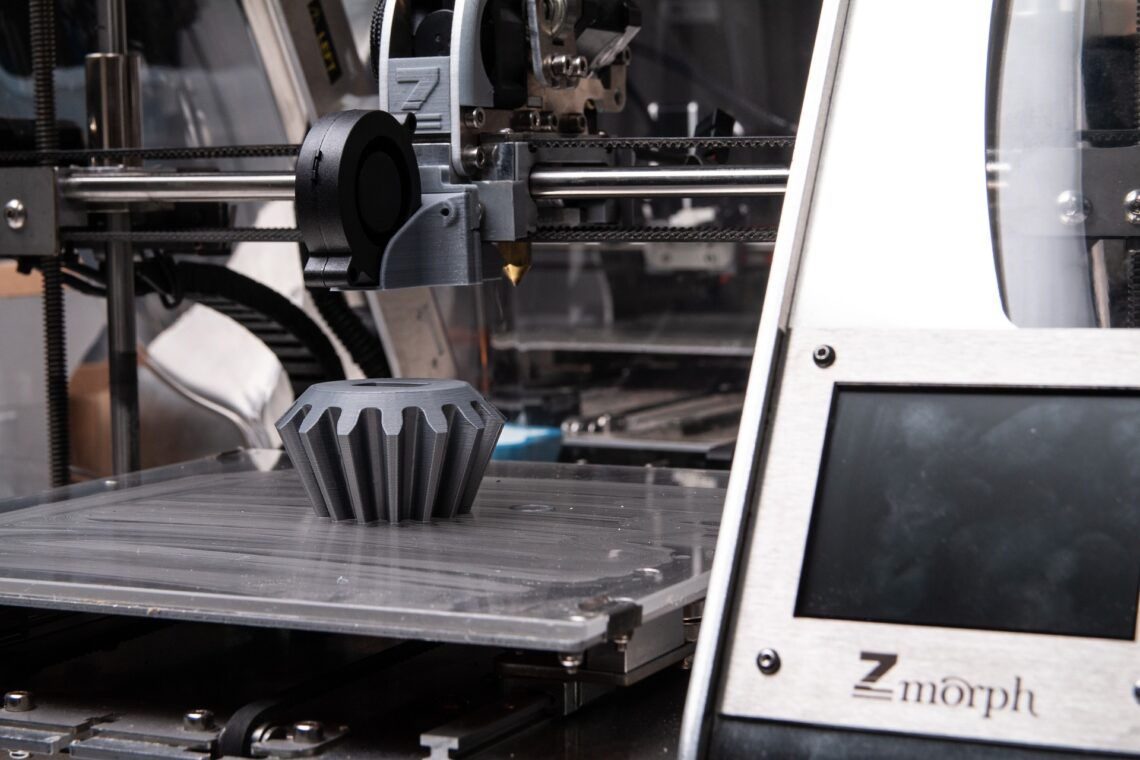
3D Printing: Transforming Manufacturing
3D printing, also known as additive manufacturing, is revolutionizing the manufacturing industry by enabling on-demand production of complex parts and customized products with unprecedented speed and efficiency. By layering materials based on digital designs, 3D printing eliminates traditional manufacturing constraints, reduces waste, and facilitates rapid prototyping and iteration. From aerospace and automotive to healthcare and consumer goods, leveraging 3D printing technology unlocks opportunities for cost savings, supply chain optimization, and product innovation, reshaping the future of manufacturing and distribution.
Evolution of 3D Printing in Manufacturing
Initially, 3D printing was primarily utilized for rapid prototyping purposes within industrial settings. Engineers and designers relied on this technology to quickly create physical prototypes of their designs, allowing for iterative improvements and faster product development cycles.
As 3D printing technology evolved and became more sophisticated, its applications expanded beyond prototyping. Advancements in printing materials, such as the development of stronger and more durable polymers, metals, and composites, enabled 3D printers to produce end-use parts with properties comparable to those manufactured through traditional methods.
This evolution paved the way for wider adoption of 3D printing in manufacturing. Industries ranging from aerospace and automotive to healthcare and consumer goods began integrating additive manufacturing into their production processes, realizing benefits such as reduced costs, increased design flexibility, and shorter lead times.
Benefits of 3D Printing in Manufacturing
Incorporating 3D printing into manufacturing processes offers a multitude of advantages, revolutionizing traditional production methods. Here are some key benefits:
- Cost-effectiveness:
- Elimination of tooling costs: Unlike conventional manufacturing, which requires costly molds and tooling for each unique design, 3D printing enables the direct production of parts without the need for specialized tooling.
- Reduced material waste: Traditional subtractive manufacturing methods often result in significant material wastage due to cutting or machining processes. In contrast, additive manufacturing builds objects layer by layer, minimizing material waste and optimizing material usage.
- Customization and Design Flexibility:
- Tailored solutions: 3D printing empowers manufacturers to create customized products that meet specific customer needs and preferences. From personalized medical implants to bespoke consumer goods, the flexibility of additive manufacturing allows for unprecedented levels of customization.
- Complex geometries: Unlike traditional manufacturing techniques, which may be limited by the constraints of molds and machining, 3D printing enables the fabrication of intricate and complex geometries with ease. This opens up new design possibilities and opportunities for innovation.
- Reduced Lead Times:
- Rapid prototyping: With 3D printing, designers can quickly iterate on product designs by producing prototypes in a matter of hours or days, significantly accelerating the product development cycle.
- On-demand manufacturing: Additive manufacturing enables on-demand production, allowing manufacturers to respond swiftly to market demands and reduce inventory costs. Products can be manufactured as needed, reducing the need for large-scale production runs and warehouse storage.
Overall, the adoption of 3D printing in manufacturing promises to revolutionize the industry by offering cost-effective, customizable, and sustainable solutions that drive innovation and efficiency.
Applications of 3D Printing in Manufacturing
Industry | Application | Examples |
Aerospace | Prototyping and production of aircraft parts. Customized tooling and fixtures | Engine components. Interior cabin components |
Automotive | Rapid prototyping of vehicle components. Production of lightweight and complex parts | Concept car models. Brake calipers, exhaust manifolds |
Healthcare | Patient-specific medical devices. Surgical planning aids | Custom prosthetics, dental implants. Anatomical models, surgical guides |
Consumer Goods | Customizable fashion and accessories. On-demand production of household items | 3D-printed jewelry, eyewear frames. Kitchen utensils, decorative objects |
3D printing technology has found diverse applications across various industries, revolutionizing traditional manufacturing processes. Here are some key areas where 3D printing is making an impact:
- Aerospace:
- Prototyping and production of aircraft parts: 3D printing enables aerospace companies to rapidly prototype and manufacture complex components, such as engine parts and interior cabin components.
- Customized tooling and fixtures: Additive manufacturing allows for the creation of bespoke tooling and fixtures, enhancing manufacturing efficiency and precision.
- Automotive:
- Rapid prototyping of vehicle components: Automotive manufacturers utilize 3D printing to quickly iterate on designs and produce prototypes of automotive parts, including concept car models.
- Production of lightweight and complex parts: Additive manufacturing enables the production of lightweight and intricate components, such as brake calipers and exhaust manifolds, optimizing vehicle performance.
- Healthcare:
- Patient-specific medical devices: 3D printing facilitates the customization of medical devices, such as prosthetics and dental implants, to match the unique anatomy of individual patients.
- Surgical planning aids: Surgeons utilize 3D-printed anatomical models and surgical guides to plan complex procedures with greater precision and accuracy.
- Consumer Goods:
- Customizable fashion and accessories: Designers leverage 3D printing to create customizable fashion items, including jewelry and eyewear frames, tailored to individual preferences.
- On-demand production of household items: Consumers can benefit from on-demand manufacturing of household items, such as kitchen utensils and decorative objects, tailored to their needs and style preferences.
These examples demonstrate the versatility and potential of 3D printing technology to revolutionize manufacturing across a wide range of industries, from aerospace and automotive to healthcare and consumer goods.
Challenges and Limitations of 3D Printing in Manufacturing
Despite its numerous advantages, 3D printing in manufacturing also faces several challenges and limitations that need to be addressed:
- Material Limitations:
- Limited material options: While the range of materials available for 3D printing continues to expand, there are still constraints on the types of materials that can be used, particularly in industries requiring specific material properties such as high heat resistance or conductivity.
- Material compatibility: Certain materials may not be compatible with certain 3D printing processes, limiting the choice of materials for specific applications.
- Quality Control Issues:
- Variability in print quality: Factors such as layer adhesion, surface finish, and dimensional accuracy can vary between prints, leading to inconsistencies in part quality.
- Post-processing requirements: Many 3D-printed parts require post-processing steps, such as sanding, polishing, or painting, to achieve the desired surface finish and mechanical properties, adding time and cost to the production process.
- Intellectual Property Concerns:
- Risk of unauthorized replication: 3D printing technology makes it easier to replicate physical objects, raising concerns about intellectual property infringement and unauthorized copying of patented designs.
- Difficulty in enforcing IP rights: The decentralized nature of 3D printing, coupled with the ease of sharing digital design files online, presents challenges for manufacturers in enforcing intellectual property rights and preventing counterfeiting.
Addressing these challenges requires ongoing research and development efforts to improve materials, enhance printing processes, and develop robust quality control measures. Additionally, policymakers and industry stakeholders must work together to establish clear guidelines and regulations governing the use of 3D printing technology to protect intellectual property rights and ensure ethical manufacturing practices.
Future Outlook of 3D Printing in Manufacturing
The future of 3D printing in manufacturing holds immense promise, with ongoing advancements poised to further revolutionize the industry. One key area of development is the expansion of printable materials, with researchers exploring new materials and composites that offer enhanced properties such as strength, durability, and biocompatibility. These materials will enable 3D printing to penetrate a broader range of industries and applications, from aerospace and automotive to healthcare and construction.
Furthermore, emerging technologies such as continuous liquid interface production (CLIP) and binder jetting are pushing the boundaries of additive manufacturing, enabling faster printing speeds, finer resolution, and larger build volumes. As these technologies mature and become more accessible, we can expect to see increased adoption of 3D printing for mass production and custom manufacturing applications. The integration of artificial intelligence and machine learning algorithms into 3D printing workflows is also poised to streamline design optimization, process control, and quality assurance, unlocking new levels of efficiency and innovation in manufacturing processes.
