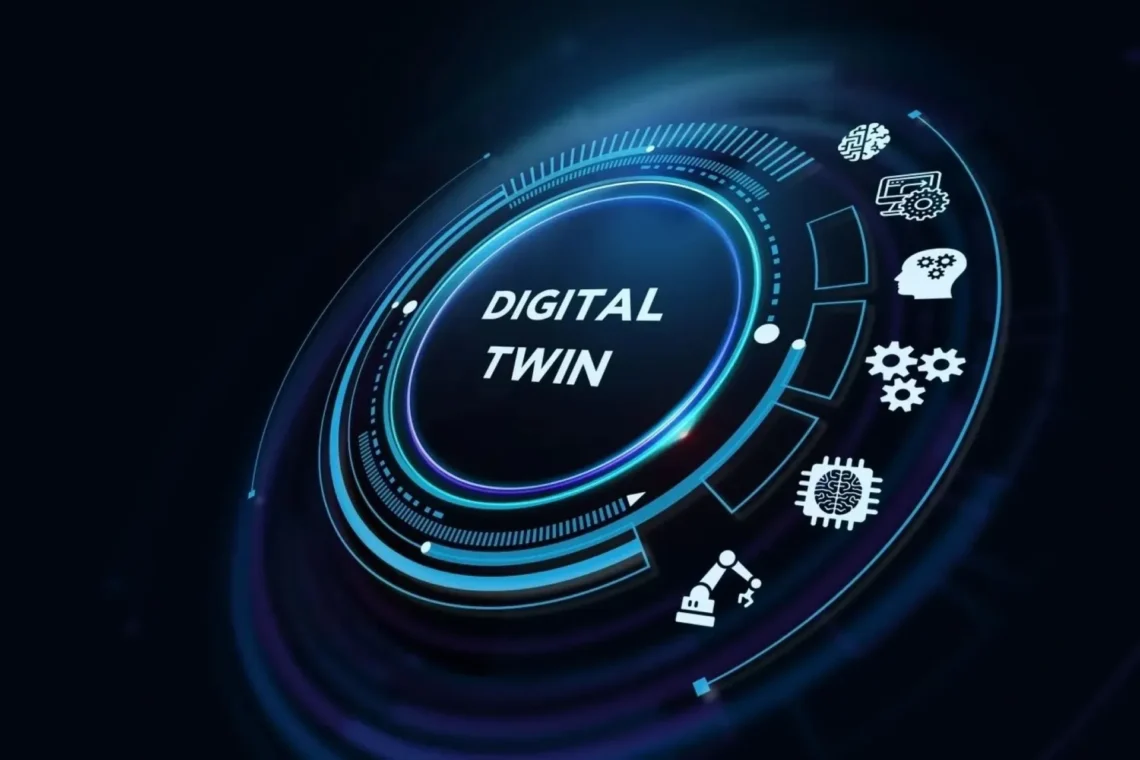
Digital Twins: Improving Product Design
Digital twins are virtual representations of physical objects, processes, or systems that enable real-time monitoring, analysis, and optimization throughout the product lifecycle. By integrating IoT sensors, data analytics, and simulation technologies, digital twins provide insights into product performance, predict maintenance needs, and facilitate iterative design improvements. From manufacturing and construction to healthcare and smart cities, leveraging digital twins enhances product quality, reduces time-to-market, and enables predictive maintenance, driving innovation and competitiveness in the digital age.
What are Digital Twins?
Digital twins are virtual replicas of physical objects, processes, or systems. They utilize real-time data and simulation models to mirror the behavior and characteristics of their physical counterparts. This technology enables businesses to analyze, monitor, and optimize the performance of products throughout their lifecycle.
In recent years, digital twins have gained widespread adoption across various industries, ranging from manufacturing and healthcare to smart cities and agriculture. They serve as invaluable tools for predictive maintenance, performance optimization, and even scenario planning. By leveraging digital twins, organizations can gain deeper insights into their operations, leading to improved efficiency, reduced costs, and enhanced decision-making capabilities.
How Digital Twins Improve Product Design
Digital twins play a pivotal role in enhancing product design processes by leveraging advanced technologies and real-time data. Here’s how they contribute to improving product design:
- Simulation and Prototyping:
- Digital twins enable virtual simulations and prototyping, allowing designers to test different design iterations without the need for physical prototypes.
- By simulating various scenarios, designers can assess the performance, durability, and functionality of products in a controlled environment, leading to more informed design decisions.
- Iterative Design Processes:
- With digital twins, product design becomes an iterative process where designers can continuously refine and optimize designs based on real-time feedback.
- This iterative approach facilitates rapid iteration cycles, shortening the time-to-market for new products and reducing the risk of costly design flaws.
- Real-time Monitoring and Feedback:
- Digital twins provide real-time monitoring capabilities, allowing designers to track the performance of products throughout their lifecycle.
- By collecting and analyzing data from sensors embedded in physical assets, designers can identify potential issues early on and make proactive adjustments to optimize performance.
In essence, digital twins revolutionize product design by enabling efficient simulation, iterative design processes, and real-time monitoring, ultimately leading to the development of higher quality products with reduced time and cost constraints.
Benefits of Digital Twins in Product Design
Benefit | Description | Example |
Cost Reduction | Digital twins help minimize costs associated with physical prototyping, testing, and maintenance by providing virtual simulations and predictive analytics. | Using digital twins, an automotive company saved millions in prototype costs. |
Time-saving | By streamlining design iterations and enabling real-time monitoring, digital twins reduce time-to-market for new products, giving businesses a competitive edge. | A consumer electronics manufacturer reduced product development time by 30%. |
Improved Quality | Digital twins facilitate thorough testing and analysis, leading to higher-quality products with fewer defects and enhanced performance. | Aeronautical engineers improved aircraft engine efficiency using digital twins. |
- Cost Reduction:
- Digital twins help minimize costs associated with physical prototyping, testing, and maintenance by providing virtual simulations and predictive analytics.
- Using digital twins, an automotive company saved millions in prototype costs.
- Time-saving:
- By streamlining design iterations and enabling real-time monitoring, digital twins reduce time-to-market for new products, giving businesses a competitive edge.
- A consumer electronics manufacturer reduced product development time by 30%.
- Improved Quality:
- Digital twins facilitate thorough testing and analysis, leading to higher-quality products with fewer defects and enhanced performance.
- Aeronautical engineers improved aircraft engine efficiency using digital twins.
Digital twins offer significant advantages in product design, ranging from cost reduction and time-saving to improved product quality. By harnessing the power of virtual simulations and real-time monitoring, businesses can optimize their design processes and deliver innovative products more efficiently.
Challenges and Limitations
Despite their numerous benefits, digital twins also present certain challenges and limitations that organizations need to address:
- Data Accuracy and Privacy Concerns:
- Ensuring the accuracy and reliability of data used in digital twins can be challenging, especially when dealing with large volumes of heterogeneous data from multiple sources.
- Privacy concerns related to data collection, storage, and usage also pose significant challenges, particularly in industries with strict regulations such as healthcare and finance.
- Implementation Costs:
- Developing and implementing digital twin solutions requires substantial investment in technology infrastructure, software development, and personnel training.
- Small and medium-sized enterprises (SMEs) may find it financially prohibitive to adopt digital twin technologies, limiting their access to these innovative tools.
- Integration with Existing Systems:
- Integrating digital twins with legacy systems and existing infrastructure can be complex and time-consuming.
- Compatibility issues between different software platforms and data formats may arise, necessitating interoperability standards and custom integration solutions.
Addressing these challenges requires a holistic approach that encompasses technological innovation, organizational readiness, and regulatory compliance. By overcoming these hurdles, organizations can fully leverage the potential of digital twins to enhance product design and drive business growth.
Case Studies
Automotive Industry
The automotive sector has embraced digital twins to optimize various aspects of product design and manufacturing. Companies use digital twins to simulate the performance of vehicles under different driving conditions, assess safety features, and optimize fuel efficiency. For example, a leading car manufacturer utilizes digital twins to conduct virtual crash tests, reducing the need for physical prototypes and accelerating time-to-market for new vehicle models.
Aerospace Sector
In the aerospace industry, digital twins are revolutionizing aircraft design, maintenance, and operation. Aircraft manufacturers leverage digital twins to simulate aerodynamic performance, analyze structural integrity, and predict maintenance needs. For instance, a major aerospace company utilizes digital twins to monitor the health of aircraft engines in real-time, enabling proactive maintenance and minimizing downtime. By harnessing digital twin technology, aerospace companies can enhance safety, reliability, and efficiency across their fleet of aircraft.
